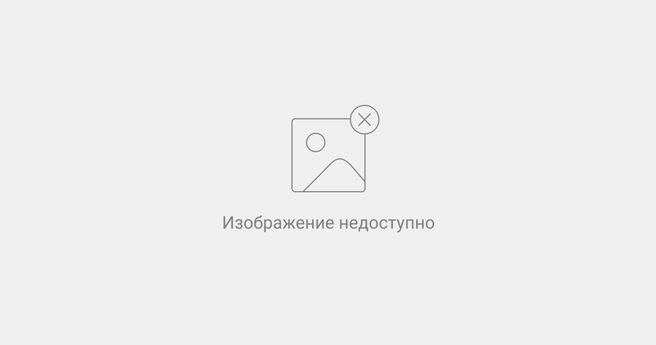
В России не хватает собственных мощностей для производства цемента. Наращивать их стране помогают зарубежные фирмы: заводы возводят и реконструируют компании из Дании, Германии, а последнее время и из Китая. Отечественные же машиностроители и инженеры зачастую остаются без работы. Почему сложилась такая ситуация и до чего борьба за выживание довела отечественную инженерную мысль, рассказывает генеральный директор ЗАО «Волгоцемсервис» Валерий Дубов.
– «Волгоцемсервис» – долгожитель среди тольяттинских компаний: его создали в 1992 году. Сейчас ВЦС помогает открывать производства другим – от разработки проектов до строительства заводов. Но как начинался ваш бизнес?
– Инициатором организации нашей инжиниринговой фирмы было производственное объединение «Волгоцеммаш». Его руководство понимало, что с появлением рынка основными конкурентами станут западные компании, в которых, кроме изготовления оборудования для производства стройматериалов, есть всё: наука, проектирование, сопровождение вплоть до ввода заводов в эксплуатацию. Мы также поставили своей целью комплексное обслуживание потребителей: хотели не только проектировать машины, но и проводить их шефмонтаж, пуско-наладку, разрабатывать технологии производства…
– Переход в рыночные условия был тяжелым?
– Для начала порвались внутрисоюзные связи, которые ранее позволяли делать кооперацию. Никто ничего не строил, не реконструировал. Задача была – выжить. Первые заказы на оборудование нам сделала цветная и черная металлургия (прежде основными поставщиками здесь были украинские заводы). А далее, когда снова появился спрос на стройматериалы, началось вторжение зарубежных фирм. И оказалось, что российское оборудование для производства цемента слишком энергоёмкое – востребованным стало импортное. Возрождение отечественного машиностроения началось лишь после дефолта 1998 года: покупать за рубежом было дорого. Пошли заказы, но именно на поставку комплектного оборудования: для нас это было ново. Создали консорциум машиностроительных предприятий (в него вошел «Тяжмаш» (Сызрань), «Электростальский завод тяжелого машиностроения» и красногорский машиностроительный завод «Бецема»), который должен был брать заказы и распределять среди членов консорциума работы. Но объединение не состоялось.
– Но ЗАО «Волгоцемсервис» всё же удалось реализовать интересные проекты.
– Да. Впервые в 1996 году мы взялись за строительство дробильно-сортировочного завода под ключ. Предприятие до сих пор работает в поселке Кикерино Ленинградской области. В целом качество, надежность и долговечность российского оборудования на самом высоком уровне. Наша цементная отрасль построена в основном с использованием отечественного оборудования. Возведены заводы в Египте, Йемене и в бывших странах народной демократии. Туда же мы до последнего времени поставляли запчасти. В 2009 году с применением отечественного оборудования ввели в эксплуатацию две новые технологические линии по производству 1500 тонн клинкера в сутки в Беларуси и 1000 тонн клинкера в сутки в Магнитогорске. Однако технология была старая, мокрая. Сухой же способ производства цемента дает предприятиям примерно 40% экономии тепла. На сегодня Запад в этом вопросе главенствует в России: датская фирма «Смит», немецкие «Полизиус» и КХД комплектно строят цементные заводы. Также стал проектировать и возводить некоторые предприятия в России Китай. «Волгоцеммаш» отошел от активного участия в поставках оборудования для цементной промышленности и вопрос комплектных поставок остается открытым. ВЦМ обратился к научным разработкам.
– Какое именно направление сочли перспективным?
– Мы пошли по пути производства тонкодисперсных материалов для строительной индустрии. Разработали новую технологию изготовления заполнителей для асфальтобетона и сухих смесей. Кроме того, энергосберегающую технологию переработки высоковлажных материалов. Она легла в основу способа переработки сырьевых материалов при производстве клинкера на «Белорусском цемзаводе» «Кричевцементношифере», а также метода помола и сушки диатомита. Высушенная эта горная порода – прекрасное биоудобрение: она повышает плодородие почвы примерно на 20%. В обожженном виде её можно использовать для очистки минерального и растительного масла, вин, дезактивации воды. По нашему проекту в прошлом году в городе Инза Ульяновской области построили цех по производству высушенного и обожженного диатомита по запатентованной технологии. Стоимость строительства оценили в 450 миллионов рублей. Продукция цеха пользуется спросом, в том числе за рубежом. Первые поставки диатомита на экспорт окупили затраты на возведение цеха.
– А за какую работу ЗАО «ВЦС» удостоили награды всероссийского конкурса ТПП РФ «Золотой Меркурий» в сфере строительства?
– За проекты, реализованные в Самарской, Челябинской, Ленинградской и других областях. Так, в Сокском карьероуправлении построили транспортируемую дробильно-сортировочную установку и установку для производства мелкого щебня. На Жигулевском известковом заводе, находящемся в зоне Самарской Луки, – помольно-сушильную установку по выпуску минерального порошка для асфальтобетона и заполнителей сухих смесей. Здесь новая технология и современная система пылеулавливания обеспечили выброс пыли в атмосферу значитально ниже допустимых норм – не более 10 миллиграмм на куб воздуха.
Премию вручал в 2008 году президент ТПП РФ, академик Евгений Примаков. Это было неожиданно и в то же время ожидаемо: прикладной науки как таковой в России практически нет, но она нужна и мы ей занимаемся, совершенствуем технологии производства стройматериалов, оборудование. В этом году мы стали лауреатами областного конкурса «Архитектурный Оскар» в номинации «Лучший проект промышленного производства».
– На какие проекты ещё делает ставку компания?
– Работаем над оборудованием, технологией и строительством установок, заводов, цехов по переработке отсевов дробления. Например, «Сокское карьероуправление» (СКУ) раньше выпускало 7 миллионов кубов щебня в год, сейчас примерно 3 миллиона тонн, но все их разбирают. Мы уже построили в СКУ дробильно-сортировочную установку, сделали специальную конструкцию для погрузки щебня в баржи. Осталось решить вопрос использования отсевов производства: их никто не покупает, приходится отвозить на рекультивацию в отвалы. Но нужно максимально использовать горную массу, подарок Земли. И мы уже построили для этого установки в Калужской, Владимирской областях, сейчас делаем для Самарской области – организовываем переработку отсевов дробления на мелкие фракции песка и заполнителей сухих смесей асфальтобетона. Кроме того, занимаемся реконструкцией дробильно-сортировочной установки в «Сокском карьероуправлении». Работаем с гипсовым заводом: запроектировали установку для добычи и переработки гипса в карьере. Сотрудничаем с Тульской, Калужской областями.
– В компетенции ВЦС и проектирование заводов по переработке твердых бытовых отходов. Востребованы ли они в России?
– Мы сделали проект реконструкции действующего завода по переработке твердых бытовых отходов (ЗПБО) в Тольятти. К сожалению, из-за недостатка финансирования дополнительную линию не построили. А ведь цель была хорошая – максимальная утилизация мусора и производство компоста. Этот проект увязывали с цементным заводом в Жигулевске. Предполагалось, что в Тольятти расширится переработка отходов, их будут везти в том числе из Жигулевска, а неперерабатываемые транспортировать на цементный завод и сжигать там в печи (экономит тепло и исключает необходимость искать место для захоронения отходов).
Увы, в России работают всего два ЗПБО: в Тольятти и в Ленинградской области. Их строительство требует больших первоначальных вложений: 10 миллионов долларов для возведения завода мощностью 500 тысяч кубов отходов в год. Поэтому заказов на них нет. Хотя, считаю, город с населением 250 тысяч человек должен иметь ЗПБО, а не мусоросжигающую установку, которая не дает вторичного сырья и наносит вред экологии.
– Каким видите будущее отечественного тяжелого машиностроения?
– Его проблемы не решены. Собираюсь предпринять уже третью попытку как-то организовать комплектные поставки оборудования для цементных заводов: никто к нам не придет и попросит отдельно мельницу или печку. Но, наверное, должна быть и воля руководства России в этом вопросе, ведь цементная отрасль, которая задаёт цены на все остальные стройматериалы, переходит полностью под контроль зарубежных фирм. В 2009 году в стране не просто снизили таможенные налоги на поставку оборудования для строительства цементных заводов, а исключили НДС. И если до этого отечественное оборудование было в полтора-два раза дешевле импортного, то сейчас оно не конкурентоспособно в ценовом отношении.
Китай в 1991 году производил 230 миллионов тонн цемента, США – 180, Россия – 220. Сейчас Китай выпускает около 2 миллиардов тонн в год. В России же делают примерно 60 миллионов тонн цемента при потребности в 90. Новые заводы и реконструкцию старых ведут зарубежные фирмы. Наши предприятия тяжелой индустрии не имеют ни одного заказа на цементное оборудование.
Оптимистично смотреть в будущее позволяет только то, что стали поступать заказы на проектирование установок для производства строительных материалов с подготовкой к универсиаде Казани: туда везут нашу щебенку, сухие смеси. Зачем ввозить из-за рубежа то, что мы можем делать сами? Стараемся это показать, расширяем некогда созданные производства.
Есть люди, которые понимают: наш инженер не хуже зарубежного. Но ещё одна проблема, что старые специалисты уходят, а смены нет. Плюс не развивается прикладная наука, которая как раз и позволяет создать новые технологии и конкурентоспособное оборудование. Поэтому давно мечтаю об инжиниринговом центре (каким раньше был ВНИИ «Цеммаш»), где бы проводились научные исследования и готовились молодые кадры. С ним бы отрасль развивалась, выпускники вузов знали, что могут найти хорошую работу в своём городе.